How AMRs Empower Your Workforce and Combat the Labor Shortage

Written by Jacob Lish
3 MIN READ
Employee turnover and recruitment costs are on the rise amongst a dwindling labor pool for warehousing workflows.
According to the US Bureau of Labor Statistics, since 2015 there has been an hourly wage increase of $0.50 to $1.00 every year with an even larger increase from 2020 to 2021. That’s without considering the basic benefits and other costs of hiring employees.
Furthermore, with the exasperated effects of the pandemic, some companies that can afford it are offering extra benefits such as free college tuition, large signing bonuses, referral bonuses, and other incentives to fill the spots they need and keep the employees they have. So how can businesses combat the strains of a labor shortage with ever increasing costs?
Autonomous mobile robots (AMRs) address these issues by providing quick deployment, high flexibility, low upfront costs, a fast ROI, and a more enjoyable working environment.
How it Works: In Theory
While the exact distance varies significantly from warehouse to warehouse, employees are walking miles per day during work hours. In some cases, it can be up to 15 miles per day per piece picker. That’s about 5 hours a day spent walking. Imagine if they could virtually cut out all the non-essential travel time by delegating material movement tasks to an AMR. It would free up the worker to spend more time on value-adding tasks while eliminating the dangers and risks associated with material movement.
AMRs aid their human counterparts by traveling to a picking zone to meet the picker that loads up the robot with an order, then the robot takes the order back to where the goods will be packaged and shipped. The employee then meets another AMR waiting nearby for the next order. The employees don’t have to do any more of the long walks and are able to move onto the next order instantly after the previous one is picked.
Not only are the employees that are already in the facility able to increase their own productivity, in many cases it leads to opportunities for them to be upskilled for other important tasks within the operation.
The facility is no longer at the mercy of increasing labor demand and costs with a dwindling labor pool. Instead, it is investing in a lasting solution for years to come that provides flexibility to grow with the company and scale up or down for peak and trough seasons. Now, the facility can focus on creating a better work environment for their existing employees and decrease labor turnover, thus saving more on the costs of recruitment and training.
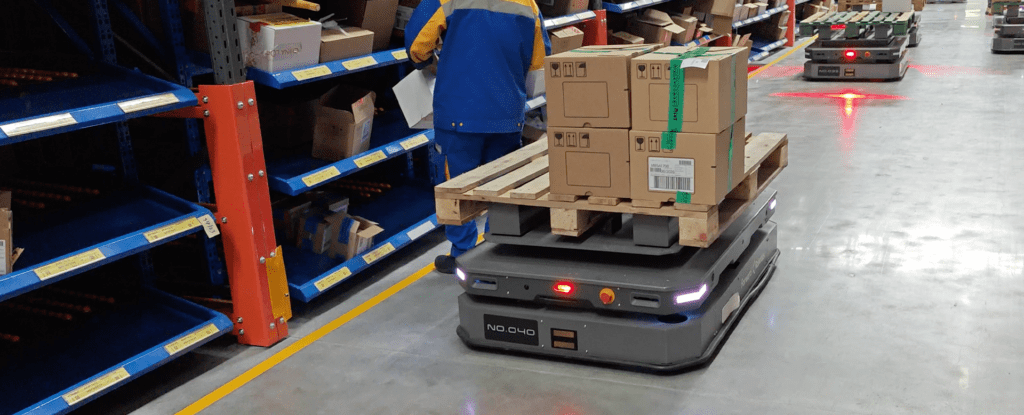
How it Works: In Practice
One of the globe’s top 10 3PL companies, JD.com, was using pallet trucks to pick thousands of cases per day. It relied heavily on its labor to move heavy cases and pallets around the facility. JD decided to go with a ForwardX solution to reduce labor dependency and double its productivity. With a fleet of Max 600 AMRs and ForwardX’s f(x) Fleet Manager connected to JD’s WCS, it was able to meet its growing throughput requirements without employing any further order pickers. So far, the AMRs have resulted in a 30% operational cost reduction for the company.
DHL partner, SF Supply Chain China, had slightly different pain points in one of their facilities. The facility handles 400 retail stores with varying delivery frequencies, creating a complex system. In order to simplify the workflows and meet the rising demand, SF DHL chose to implement a ForwardX Flex 300-S fleet with custom-built racking and f(x) Fleet Manager. It saw immediate results and tripled its units picked per hour while seeing a 43% reduction in operational costs.
ITOCHU Logistics China chose to implement a ForwardX Flex solution to automate picking and packing workflows in its Tianjin location. The Flex solution consisted of a fleet of Flex 300-R AMRs combined with f(x) Fleet Manager software. The solution was designed to minimize travel, reduce cognitive fatigue, lower labor dependency, and allow for rapid scalability. After implementation, virtually all long walks were eliminated, in-aisle walking was significantly reduced, and order checks became irrelevant. ITOCHU saw a 52% operational cost reduction by increasing productivity and decreasing its error rate.
Empower Your Workforce
Rising recruitment costs don’t have to mean higher overall costs for a business. The employees can benefit from higher wages, safer working environments, and less mundane work by working side by side with AMRs. All while the company gets to benefit from lower overall costs on its operations. ForwardX AMRs decrease labor costs and labor dependency while creating a more enjoyable working environment for everyone involved.
Reach out to us to start your automation journey: Contact Us.