Max 600-L AMRs are assigned to pick empty pallets and take them to the designated picking points. Here, the AMRs collaborate with human workers who use PDAs to receive picking assignments, print labels, scan barcodes, load items, and verify items. A handheld Bluetooth printer makes the on-site printed labels possible. After loading, the AMRs transport the pallets to the unloading area, where they are either packed or directly moved to outbound logistics.
99.5%
ERROR-FREE OPERATIONS
WORLD’S 1ST
5G AMR DEPLOYMENT
20%
OPERATIONAL COST SAVINGS
30%
INCREASE IN THROUGHPUT CAPACITY
TCL Solution
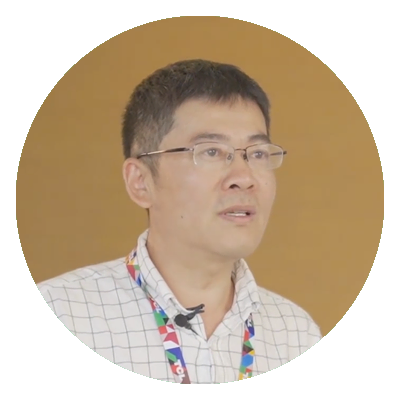
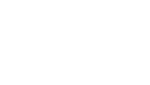
TCL’s Head of President’s Office, Caijun Zhao:
“Last year, we cooperated with ForwardX on a project as part of our 5G digital transformation initiative. Our aim was to achieve unmanned material handling across the factory. The project has been successful so far with seamless collaboration between the AMRs, workers, machines, and loading carts. The project is delivering great results for us and helping us to achieve our goal of automating material handling and replacing low-value work with intelligent automation. So far, we’ve been able to repurpose 34 workers, from planners and dispatchers to front-line managers.”