Challenge Us to Move Your Parts — Solving Complex Automotive Intralogistics from Roof Systems to Car Doors
Tier 1 suppliers are under pressure to move more parts, more quickly, and with greater precision than ever before. As automotive manufacturing grows increasingly complex, intralogistics solutions must adapt to handle a wide range of components — from delicate electronics to heavy mechanical assemblies — across multiple workshops, in real time.
ForwardX Robotics is tackling this challenge head-on with one of the largest known deployments of autonomous mobile robots (AMRs) in automotive sector: 435 AMRs are now live at Chery’s Dalian factory, transforming internal logistics and setting a new benchmark for scalable, intelligent automation in the industry.
Tailored AMRs for Tier 1 Complexity
To meet the evolving needs of Tier 1 suppliers, ForwardX’s solution includes three specialized AMR models that work together to streamline movement across the entire factory floor:
• Flex Series AMRs: Agile units ideal for transporting small, fragile components like circuit boards and wiring assemblies with just-in-time precision and minimal floor congestion.
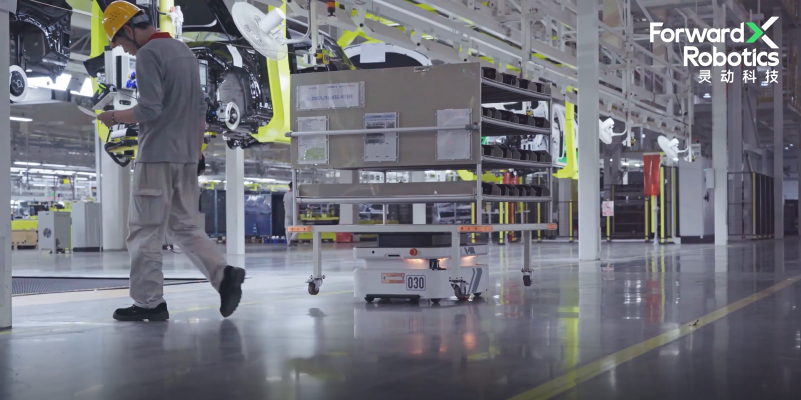
• Max Series AMRs: High-capacity robots designed to move heavy items such as engines and machinery parts, synchronizing seamlessly with production lines to eliminate delays.
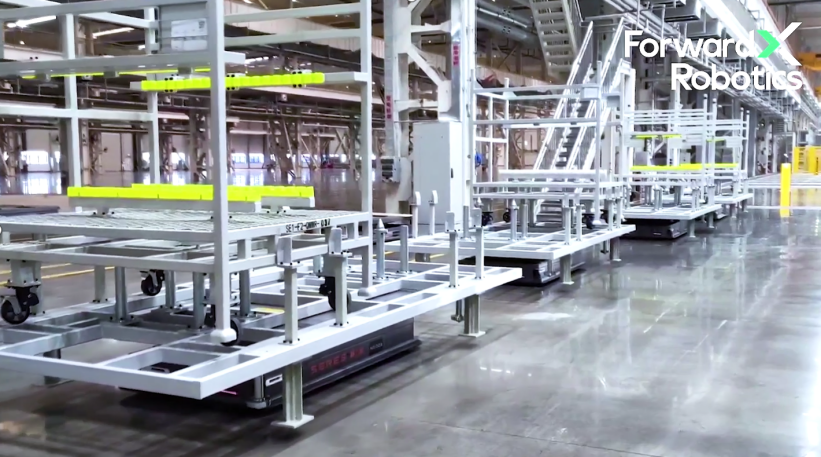
• Lynx U1000 Towing AMRs: Purpose-built for towing larger racks and bulky materials, fully integrated with Chery’s SPS system for autonomous delivery across key production zones.
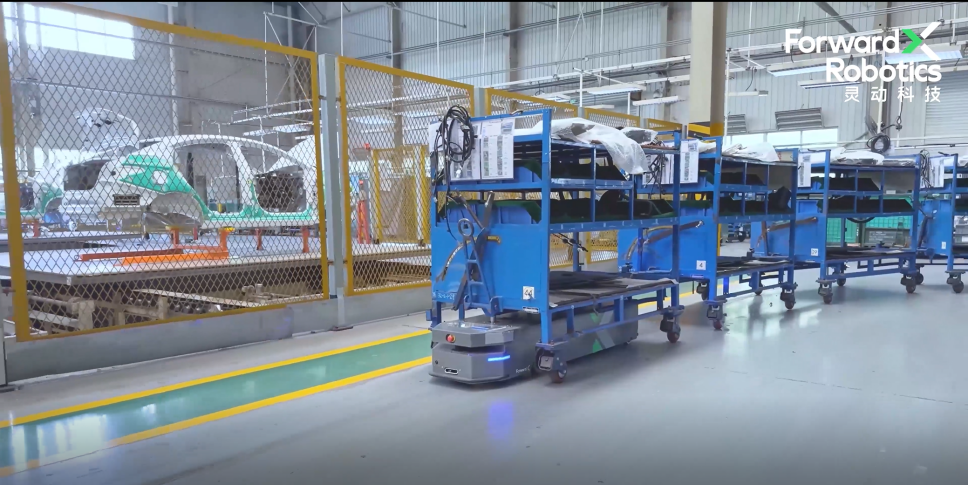
“This deployment reflects our commitment to solving real production pain points at scale,” said Nicolas Chee, CEO of ForwardX Robotics. “Chery Automobile challenged us to streamline material flow in one of their most complex facilities — and with 435 AMRs working in harmony, we’re delivering a new era of intelligent intralogistics.”
Seamless Automation Across Multiple Workshops
The result? A synchronized flow of materials — large and small — across stamping, welding, battery, and final assembly workshops, with minimal disruption and maximum uptime. Chery’s factory can now support a vehicle rollout every two minutes, powered by autonomous logistics that adapt in real time.
Proven Across the Automotive Supply Chain
ForwardX’s technology has been successfully deployed at other leading manufacturers across Asia, highlighting its versatility across diverse workflows and factory environments:
• At Inalfa, Max-1500L AMRs excel in constrained roof system workshops, moving heavy loads through tight paths with precision.
• With BYD, Tailored Forklift AMRs featuring 2.4m forks automate material movement inside high-demand EV battery facilities, safely navigating hazardous spaces.
• At Dongfeng Auto, Lynx U1000 AMRs handle car door transport inside the welding workshop, keeping pace with high-speed production lines.
These projects illustrate ForwardX’s strength in solving both general and highly specialized intralogistics challenges — from large rack movements to delicate component handling — all with flexible, scalable robotics that integrate into existing operations.
Meet ForwardX at Automate 2025 — Booth #5632
ForwardX is redefining what’s possible in automotive intralogistics. Whether you’re producing EVs, components, or complete vehicles, our AMRs are built to move your parts with speed, precision, and safety.
Join us at Automate 2025 in Booth #5632 to experience the future of automotive logistics.